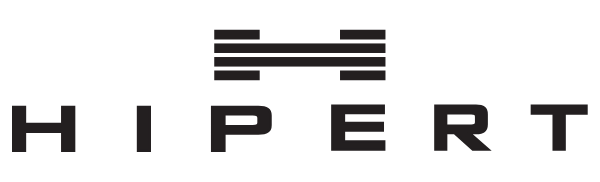
Hipert SRL is a spin-off from the University of Modena and Reggio Emilia, Italy. It was initiated in 2020 by Prof. Marko Bertogna and emerged from the HiPeRT laboratory, where research groups were seeking to exploit the performance/power of parallel processing platforms in a predictable manner, and in application contexts in which temporal constraints are critical. Based on their experience in the robotics sector, Hipert SRL can implement autonomous automated systems that perceive the environment, plan appropriate actions, and safely implement appropriate actuation commands, all in real time.
Extensive experience in full stack automation solutions enables Hipert SRL to create high-level automated systems in diverse spheres of application. As an academic spin-off with close ties to the laboratory of the University of Modena and Reggio Emilia, Hipert benefits from specialized skills in controlling complex automated systems, real-time embedded systems, deep learning, and machine learning techniques, with particular interest in genetic algorithms and reinforcement learning.
Hipert's team have extensive experience in the control of complex vehicles in a wide variety of contexts, including on-road, off-road, aerial, and maritime. Hipert's staff are specialized in the optimization of complex algorithms to run real-time on the latest generation embedded platforms. Examples of control systems designed for complex vehicle platforms include model predictive control techniques, non-linear control, and discrete/continuous optimization.
Their specific interest involves the parallelizing/optimization of these algorithms on heterogeneous parallel computing platforms, small in size and low in energy consumption, to simplify integration into mobile agile high-performance systems. This experience will be used to tackle the problem of real-time control of tensegrity structures to dynamically regulate operative configuration using scalable and high-performance algorithms, optimizing latency.
Latency is a fundamental factor for controlling these devices, which enable rapid adaptation of automated tensegrity systems to the typical dynamics of use scenarios. Accurate modeling of the control problem and correctly identifying the forces and tensions in play make it possible to optimize the dynamic reconfiguration strategy for tensegrity structures, with real-time actuation of system nodes for reliable and effective orientation of automated systems.